Damasteel® vs. Damascus Steel - Explaining the Materials
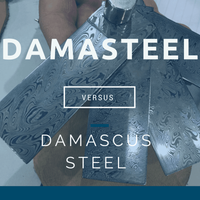
by Larry Connelley
For those looking for a damascus steel knife, you might notice another steel called Damasteel®. What's the difference, and which one makes a better blade? The difference really comes down to the manufacturing process of the two steels, and the different properties that come out of it. The short answer is that Damasteel is a proprietary process of creating damacus steel. Let's take a closer look...
Traditional Damascus -
In the traditional process of creating damascus steel, a blacksmith will weld and press two types of steel into layers. In forging, the steel is folded repeatedly, until there are as many as 100 or more layers in the piece. Damascus steel has a pattern that goes through the entire material - not a superficial exterior pattern - a common misconception for damascus steel. Both Damasteel and Damascus steel are "real".
Today, steelmakers still use this technique using two to five alloys through the pattern welding process, a process that starts off with the creation of a billet (a series of layered metal bars). The billet is heated, hammered, and folded repeatedly. The distinct patterns on the blade are created by twisting, folding and drawing out the billet. Overall, the process creates a very strong blade, but its durability is due to the steel alloys that are chosen to create the blade. Depending on the steels/metals used, damascus steel can be stainless or not. To become a stainless steel damascus both steels must have at least 14% chromium. The pattern in damascus steel is only visually revealed once the steel is cleaned, prepared and etched in acid. The two types of steel react differently in the acid oxidation process. One oxidized steel is lighter and the other is darker, only then is the pattern revealed on the surface that is hidden within the steel.
Damasteel® -
Damasteel is a modern, trademarked as well as patented powder steel process of making damascus steel. Damasteel (also the name of the company) is located in Söderfors, Sweden, a village with a long history of forging damascus steel. In fact, the steel industry began in Söderfors in 1676! The process of creating damasteel was developed in 1992 by Swedes Per Billgren, and employee at Erasteel, and knifemaker Kaj Embretsen. Damasteel takes the traditional forging process of damascus steel--and a history of steelmaking since the viking times--to the next level by using powder metallurgical steel manufacturing.
Damasteel® Manufacturing Process -
Damasteel starts with a gas atomization steel making process. Molten steel is forced through a nozzle and aerosolized. The resulting steel powders are created in a perfectly spherical shape with a high level of cleanliness and homogenous distribution of carbides (provide the cutting capabilities). The powders are then collected in a canister, which is sealed, compacted, and bonded (densified) by a process called Hot Isostatic Pressing (HIP). After the HIP process, the size of the steel material is reduced by roughly 30%. There are no welds in the steel making it structurally an extremely strong steel.
Afterwards, the capsule undergoes forging, texturing rolling in a specific way to obtain various patterns. This phase of creating patterns is extremely similar in both techniques. Damasteel comes in wide variety of patterns including ladder, rose™ (raindrop), Dense Twist™, Dden's Eye™ - some completely unique and trademarked by damasteel.
Damasteel® Composite Steels -
A benefit of the particle metal process, the damasteel includes less impurities and will contain far less inclusions than traditional damascus steel. Damasteel also carries the properties of the particle steel alloys RWL 34 and PMC27 steel. RWL 34 is a Swedish-made knife steel named after legendary knife maker Robert 'Bob' Loveless and is most similar to CPM 154 and chemically similar to ATS 34. RWL 34 steel is made by the Damasteel company. When etched, the RWL 34 is the lighter color pattern in the damascus. The second steel in damasteel is PMC27 stainless steel alloy. PMC27 is also made in Sweden. When etched is the darker pattern bands of the damascus. Both of these composite steels are manufactured using the particle metal (PM) process and provide increased toughness and edge retention compared to conventionally made steels.
Conclusion
Overall, BOTH damascus steel and damasteel have the beauty and artistry that makes damascus steel famous, and with the strength and durability both are known for. Damasteel however might be a better option when you are looking for high-performance damascus, or if you are looking for stainless quality as some traditional damascus is not stainless (because they utilize carbon tool steels). The patterning of damasteel® has somewhat of a different look (created by the HIP process) from traditional damascus and the resulting visual patterns/styles is distinctive. These two categories of damascus steels patterns are varied and a matter of individual taste - but I absolutely love both.
of note: Damasteel has been used on high-end watches, jewelry, buckles, gun barrels, writing pens and a wide variety of applications. Some knifemakers that use Damasteel extensively are: Brian Tighe, Rod Olson and LionSteel Knives.
Special Thanks to Per Jarbelius, Chairman of Damasteel, for providing input for this article.