CPM MagnaCut is the latest in American-made wear-resistant and premium particle metallurgy stainless tool steel for knives. Magnacut is an extremely tough stainless steel with excellent edge retention properties and outstanding corrosion resistance. What makes this stand out from the rest? Let's take a definitive look at the development, process, and all things CPM MagnaCut.
MagnaCut is a specifically created steel alloy for knife making and offers significant benefits for cutting tools. Specifically created for knife making, CPM MagnaCut (simply referred to as Magnacut) is stainless steel made in the USA using the CPM (particle metal) process. ‘Magna’ in Latin means great or awesome. And the "cut" harkens to the Vanadium Alloys Steel Company (VASCO) that pioneered other high-speed steel using a similar naming convention.
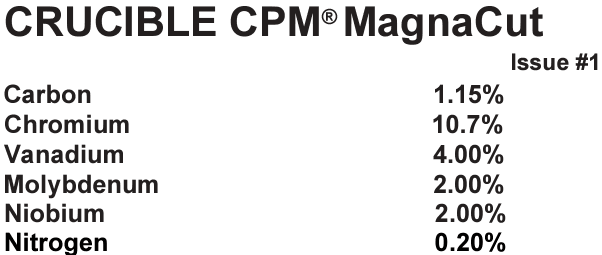
Who Developed MagnaCut?
The developer of CPM MagnaCut is Dr. Larrin Thomas. He is no stranger to the knife world. Larrin Thomas' father is a noted damascus steel smith Devin Thomas, and his childhood experiences around knives are what inspired Larrin to become a career metallurgist.
Larrin originally only had a passing interest in steel and knives but after going to a custom knife show with his father, his perspective changed. Various knifemakers were claiming their steel was “the best”. But where does the truth lie? He commented, “I wanted to know who was telling the truth!”
Wanting to know more about why certain heat treatments and steels were better than others, Larrin Thomas earned his Ph.D. in Metallurgical and Materials Engineering at the Colorado School of Mines in Golden, Colorado. He currently works full-time in the automotive steel industry and runs a website (knifesteelnerds.com) exploring the world of knife steels - in impressive technical detail.
Thomas commented to us, "I've been interested in knives and steel since I was a teenager because of my dad, Devin Thomas, who is known for making stainless Damascus steel and kitchen knives. I was very excited about developments like S30V which was a steel developed for the knife industry. I eventually got a PhD in Metallurgy and I develop automotive steels professionally. But as my hobby, I study and write about knife steel, heat treating, and engineering of knives. I had some ideas about improved knife steels and I successfully convinced Crucible and Niagara Specialty Metals to try it out."
He also wrote a best-selling book entitled 'Knife Engineering: Steel, Heat Treating, and Geometry'. Dr. Thomas's unique interdisciplinary approach in both custom knives and academic metallurgy background is a significant asset to his work and is a key reason that Magnacut was developed.
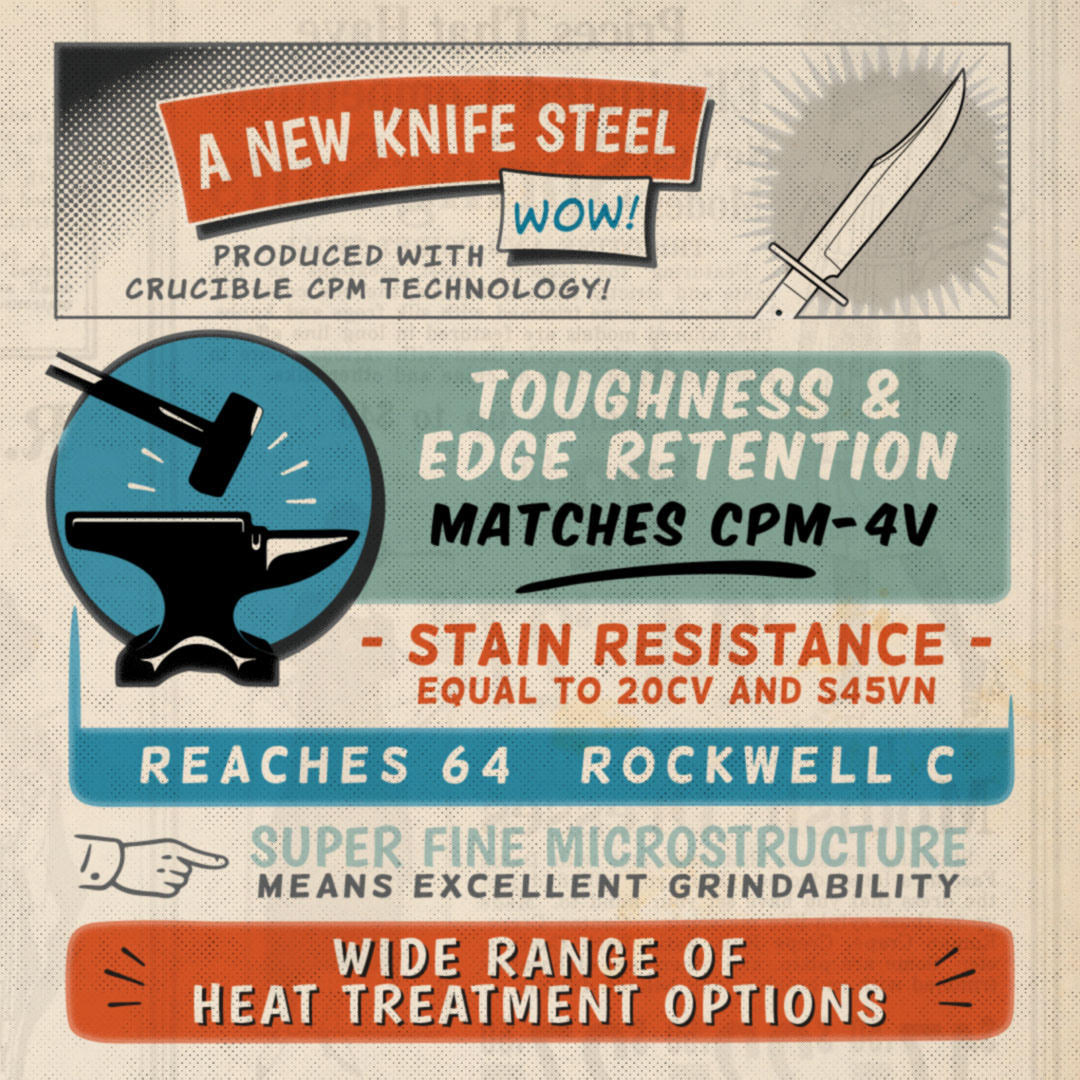
Why and How Was MagnaCut Developed?
Dr. Thomas's idea for developing MagnaCut was to create high-performance steel in stainless particle metallurgy steel. He states how anyone can have the idea to use certain elements, but it's the research and science behind it that allowed him to create something special.
According to Larrin, "The main goal of this steel design was to have much greater toughness than previous powder metallurgy stainless steels."
It is my opinion that Magnacut was highly successful in meeting the much higher toughness with the added benefit of extreme corrosion resistance.
Who Makes MagnaCut and What Process Is Used?
Magnacut is manufactured by Crucible Industries in Syracuse, New York by the United Steel Workers of America. While Crucible typically uses in-house engineers, when approached by Thomas they were intrigued. Considering he is one of the world's leading experts on knife steels, they were impressed by the research and saw the potential of the new allow, a bond was formed and MagnaCut went into production.
As far as the process, there is a major difference in MagnaCut. The major component is, after its final heat treatment, the relative lack of chromium in the alloy mix. This does something unique - it allows vadium and niobium to form more carbides in a fine microstructure of the cutting edge and allows the chromium to be more present in the steel matrix for stain resistance.
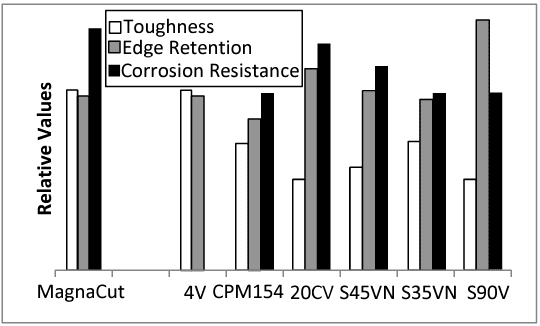
According to Dr. Thomas, "MagnaCut offers a higher level of toughness, wear resistance, and corrosion resistance than previous stainless knife steels. This makes it very versatile with a wide range of knives. The high toughness and potential hardness makes it very good for thin folders and kitchen knives. That same toughness is also great in "hard use" blades. And the excellent corrosion resistance means low maintenance and the steel even does fine with occasional exposure to saltwater."
Toughness
This stainless steel has toughness on par with some of the most impressive tool steels, like CruWear, CPM 3V, and CPM 4V. This is stainless steel that can take a beating at a level that has only been experienced on more niche steels like 3V and 4V. According to Thomas, “The new design eliminating chromium carbides gives MagnaCut a much better edge retention-toughness balance than previous PM stainless steels, and performs similar to the best non-stainless PM steels.” The presence of smaller and harder vanadium/niobium carbides, along with the CPM process, provides increased strength while eliminating the larger and more fragile chromium carbides.
Thomas Commented, "One of the main innovations of MagnaCut is it is designed to mimic the microstructure of the best non-stainless steels like Vanadis 4 Extra and CPM-4V. The chromium content was reduced in combination with balanced carbon content so that all of the chromium is "in solution" for corrosion resistance while avoiding the formation of chromium carbides. A large chromium carbide content is found in other powder metallurgy stainless steels which reduces toughness and corrosion resistance. Instead, MagnaCut only has small, high hardness vanadium and niobium carbides which leads to a better balance of toughness and wear resistance. "
Edge Retention
Due to the high hardness of the MagnaCut, the edge retention is excellent. According to industry standardized CATRA edge retention testing, Magnacut holds an edge in the range between S35VN and S45VN steels. MagnaCut easily bests those two types of steel in toughness and corrosion resistance. There is also anecdotal evidence that Magnacut is easier to sharpen, likely due to the finer vanadium-cutting carbides.
Corrosion Resistance
A huge surprise and added benefit with Magnacut is the extreme rust resistance. In my opinion, it is the highest performing very-stainless steel on the knife market. Magnacut should be the steel of choice for wet, humid, or coastal environments. It provides the user with a first-class edge retention and amazing toughness in a highly rust-resistant material. If you live on the coast or in the tropics, Magnacut would be my choice for heavy-use knife steel. According to Thomas, "Chromium is what makes stainless steel stainless, it forms a chromium oxide layer at the surface which prevents rust."
Heat Treatment
Due to its toughness, the recommended heat treatment of MagnaCut is on the high-end of hardness for knife steels. It ranges between 60-64 HRC. According to the Crucible steel datasheet, the optimal balanced heat treatment with a balance of toughness is 62.5 HRC. For some Japanese kitchen knives, where edge toughness is less important, Thomas indicates that MagnaCut can be heat treated to 62-64.
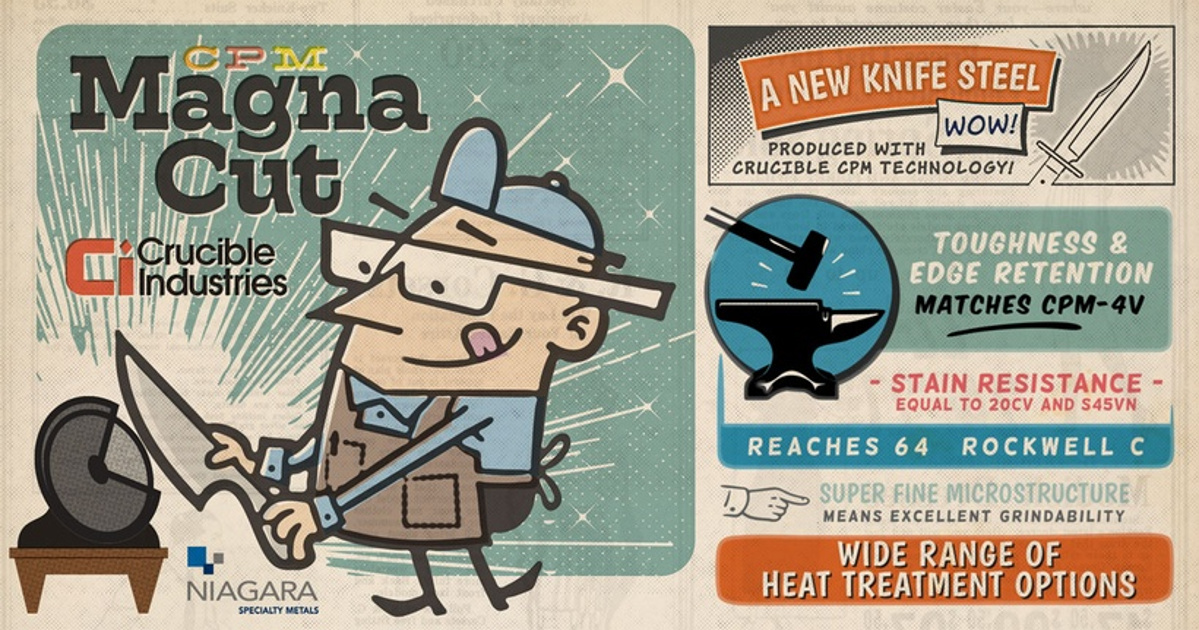
Is MagnaCut a Stainless Steel?
Yes! There are many advantages to the CPM MagnaCut, and one of them is its amazing resistance to rust, stains, and corrosion. MagnaCut is extremely corrosion-resistant yet has a relatively low chromium content of 10.7%. This is due to a high level of chrome in the steel matrix, not in the carbide form. This frees up the available chrome to create a protective chrome oxide layer on the surface of the steel. All of these features mean it's perfect for a variety of uses, including outdoor activities, survival, wet and coastal environments.
What Does CPM Stand For?
CPM stands for Crucible Particle Metallurgy. This is a proprietary trademarked name for a specific process known as Powdered Metallurgy (PM) steel. CPM makes steel very homogenous steel. This is done using a complex and expensive process of manufacturing. This process allows for an even distribution of carbides. The CPM steel-making process makes stronger steel with less likelihood of failure or variation in the final product. This means it is less likely to chip, fracture, or break in a weak spot in the microstructure of the steel.
Magnacut is perfectly suited for wet, humid or coastal environments where you also desire excellent performance and toughness. In the past, knife users have had to sacrifice performance when choosing a highly rust-resistant knife, now with a knife in Magnacut, the user gets the benefits of a very high-quality cutting tool without making a sacrifice for outstanding rust prevention.
MagnaCut vs S45VN Steel
When comparing the two, MagnaCut beats S45VN steel in toughness and corrosion resistance. In edge retention, you'll see a slight advantage with the S45VN steel but Magncut should perform better than S35VN (previous generation of S45). Keep in mind that MagnaCut has a larger percentage of vanadium carbide and the vanadium carbides are the finest and hardest carbides in knife steel. In S45VN, the highest ratio is chromium carbide. Magnacut should be easier to sharpen, seldom rust, and be extremely tough when compared to S45VN. Much more stainless and chip resistant but will hold an edge just slightly less than S45VN.
MagnaCut vs M390
In toughness, the MagnaCut is significantly tougher. But in edge retention, the M390 just edges out (pun intended) the MagnaCut. Both are highly corrosion resistant but Magnacut is the winner in rust resistance. If you plan on putting your knife through heavy, hard use, I would recommend Magnacut. With Magnacut you can increase cutting ability when compared to M390 by reducing edge thickness… more on that below.
MagnaCut - A call to thinner edge geometry
Because MagnaCut has such high toughness levels, a knife blade can be made considerably thinner without the worry of failure. Using less stock thickness at the edge means you can make a lighter knife that cuts with less force than other knives. When you can create a product with less weight and material, you can drive significant benefits to the end-user.
MagnaCut, like carbon fiber, has a very high strength-to-weight ratio. We have championed the use of carbon fiber as a structural component in knives for this exact reason. If the material is stronger and lighter, it saves energy and makes a knife more everyday carry friendly. While there is often a misguided psychological belief that heavy equals quality, when it comes to advanced materials lighter-yet-stronger should be a guiding principle.
According to Crucible's datasheet, "The excellent toughness results indicate that CPM MagnaCut is very resistant to chipping and breaking. In knifemaking, the high toughness makes it especially good for bigger blades. And fine cutting knives can have thinner edges for better cutting ability with reduced risk of chipping."
Magnacut for Knifemakers - Heat Treat and Finishing
Thomas remarked to us, "My article on Knife Steel Nerds and the datasheet both have heat treatment recommendations. The datasheet has a "recommended" heat treatment which is the relatively foolproof recommended temperature cycle that is difficult to screw up. If a knifemaker is experienced in cryo processing and pushing for higher hardness you can modify the cycles from there for high performance blades. Grinding and polishing MagnaCut is similar to other CPM S-series steels like S35VN and non-stainless steels like CPM-4V. Polishing is more difficult than steels like CPM-154 and AEB-L; the ease in finishing and polishing is part of why those two steels are very popular with custom knifemakers."
Conclusion
The CPM MagnaCut technology took years of hard work from an interdisciplinary expert (Thomas) and a US-based steel manufacturer (Crucible). Due to this collaborative hard work and expertise, we can take advantage of Magnacut with incredible toughness, excellent edge retention, and one that is highly resistant to corrosion. Magnacut is THE next-generation balanced knife steel and will see considerable adoption in 2022 and beyond.
Magnacut Links
For more in-depth information on Magnacut please visit: Magnacut at KnifeSteelNerds.com / by Dr. Larrin Thomas
For the CPM Magnacut Steel Data Sheet: CPM Magnacut Steel Data Sheet PDF by Crucible Industries
Purchase CPM Magnacut Steel at: Niagra Specialty Specality Metals
If you are a YouTuber, be sure to watch the excellent channel Larrin Thomas / KnifeSteelNerds Channel on YouTube
We purchased the book! I think you should as well Knife Engineering: Steel, Heat Treatment and Geometry ( Amazon Affiliate links)