KnifeArt: What is the definition of steel?
Beckman: Well, steel in its simplest definition is iron and carbon. It’s used generally for the blade material. Steel provides certain properties that knife makers want to have in a blade material. Steel is generally a better metal system than, say, titanium or aluminum to get the properties a knife maker wants.
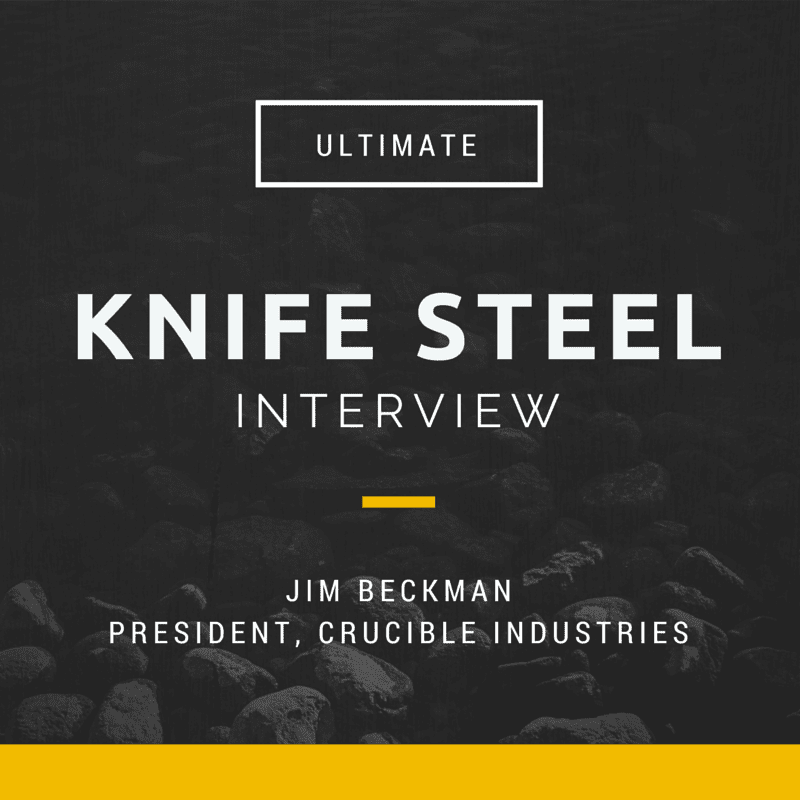
KnifeArt: The principle elements of steel are iron and carbon. There are other elements in knife steel alloys, can you go through some of the other elements and talk about why you add those to this alloy mixture?
Beckman: Okay, the basic steel would be 1095. 1095 is essentially iron plus 1% carbon. So when it is heat treated you are going to get whatever the hardness of the knife is, but the only carbide you are going to have are iron carbides and they are not going to look like the pictures, and they are not going to be particularly hard. Then you go to alloy tool steels and you are going to start seeing carbon, chrome, vanadium, molybdenum, tungsten and other elements.
Chromium: So we have already said what carbon does: carbon forms carbides and it also dissolves into the background matrix. The background matrix is generally what makes the hardness of the steel. For a corrosion resistant alloy, chrome at 11% is all dissolved in iron and provides very good corrosion resistance. The chrome over 11 or 12 % then forms chromium carbides. So you now have iron, carbon and chrome.
Vanadium, Molybdenum and Tungsten: What makes better wear resistance? Carbides. So we have chromium carbide, you can start adding more alloying elements. You can add moly, vanadium and tungsten and you will form vanadium carbides, tungsten carbides and moly carbides. The most wear resistant of these carbides are vanadium carbides. Tungsten and moly are added for carbide formation, and also to provide other properties to the alloy like toughness and hardness.
The fundamentals of chrome is corrosion resistance (and chrome carbides) but the basic fundamentals of tungsten, moly, and vanadium is in the form of carbides. Vanadium carbides have the best wear resistance because they are the smallest carbides. These combinations of all those elements give you the recipes that some people like and some people don’t.
We did some research on this and we found that if you substituted niobium for vanadium the niobium carbides seem to be a little smaller than vanadium carbides and seem to help toughness so the difference between S30V and S35V is that S35V has niobium in it substituted for some vanadium. So those are the basic elements that are in knife steels that we produce.
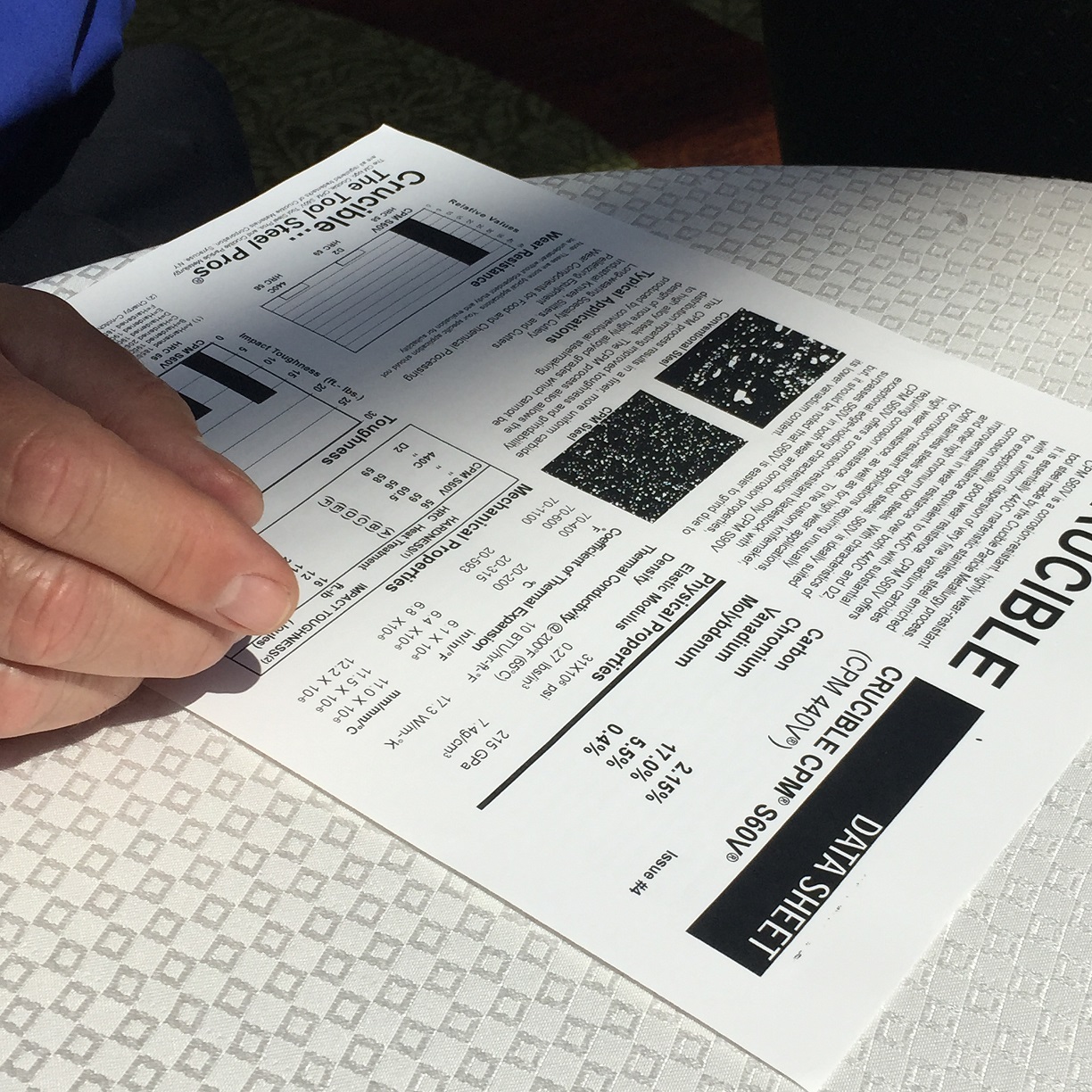
KnifeArt: What is crucible particle metal (CPM) technology and why is it important in the knives that use CPM steel?
Beckman: CPM stands for Crucible Particle Metallurgy which was invented by Crucible in the early 1970s. The first production facility in the world opened up in Syracuse, New York in 1970. The process was patented. The original market for CPM was in the cutting tool industry to take the place of some high-alloy, high-speed steels where either the carbides were too big to make a really good tool or you couldn’t get enough alloying elements into the conventionally melted materials, which you could do with the CPM process.
In terms of knife steels, CPM moved into the knife market much later. As I said originally cutting tools were the first market, the second market was what’s called cold worked (an example would be a punch) and the third major market was in plastics manufacturing for extrusion barrels, tips, screws, and things of that nature.
What caused Crucible to get into some corrosion resistant materials, with knives it is an advantage, is that the resins that were used in the plastics industry became more corrosive. The first alloy that we invented to be corrosion resistant was an alloy called CPM 440V. It also happened to be one of the early corrosion resistant wear resistance steels that started out being used in the knife industry.
In our research lab in Pittsburgh (part of Crucible up to 2009), we started developing steels primarily for the plastics industry where corrosion resistance and wear resistance were important properties. We found that we could get very good feedback from knife makers regarding properties such as wear resistance, toughness, hardness, and corrosion resistance.
So, there was a parallel development of alloys that we developed for plastics that worked in the knife industry, and these are great steels such as S30V, S35VN, S90V along with the original one S60V.
Another development for use of CPM as a knife was to take some of the alloys that were used for the cold worked industry; steels like 9V, 10V and the more current version would be 3V. So we moved some of these alloys from another market into knives.
We also moved existing air melted alloys into CPM production. The two best examples of moving existing steels into CPM would be D2 and make it a CPM D2 and the other is to take 154CM and make it CPM 154CM. The key benefit of CPM is going from very large carbides to very small uniform carbides. Both CPM D2 and CPM 154CM alloys have been successful in the knife business.
So the first path was steels developed primarily for plastics industry that had corrosion resistance. The second was to take existing wear resistant alloys and use them for knives. The third path was to take existing conventional materials and make them with the CPM process. So those were the three paths that we had taken to go from the beginning of CPM and how it evolved into being used in the knife business.
KnifeArt: At the most basic level can you describe how CPM steels are manufactured?
Beckman: All steels start with melting. Our heat sizes for steel are about 3 tons made in an air induction furnace (AIM). We add scrap, we add recycled materials, purchased ferro-alloys and we melt it- the temperatures can approach 3,000F for liquid steel. Once it’s fully melted, we adjust the chemistry to meet the alloy we are making. Then we pour the liquid steel into a tundish which has a filtration system. At the bottom of tundish is a nozzle, as the liquid steel goes from the tundish into the nozzle and exits the nozzle, and it is hit by high velocity nitrogen gas. This process is called nitrogen atomization. What atomization simply means is to take something liquid and turning it into powder particles. The power particles start solidifying and they fall about 20 feet in a stainless steel chamber into a pool of liquid nitrogen. The liquid nitrogen cools the powder. We drive off any moisture in the raw powder, we screen it and we put the powder into carbon steel canisters. We evacuate the canister and heat it at the same time and then press it from all sides in a process called HIP (Hot Isostatic Pressing). For our most common canister size- the canister starts out being 14¾ inch diameter and perhaps about 56 inches of height before HIPing and weighs about 1 US ton. After HIPing, it is about 13½ inch diameter and about 48 – 50 inches tall. Once it goes through the HIP process it is fully densified. We then take the steel and process it like any steel mill would process a steel ingot for the market.
In the knife industry we take that steel canister, process it by hot working to a slab that is approximately 4 inches thick by maybe 12 inches wide then we remove the carbon steel can material, so all that is left is the CPM steel product. It is then rolled it into sheets for the knife industry by our partner Niagara Specialty Metals.
KnifeArt: What is the key advantage to CPM technology for knives?
Beckman: If you look at the steel datasheet, this is a picture of conventionally melted product and one of CPM product. This is the microstructure of the steel, so this might be at about 200-300 magnification. The white areas are carbides and black background is tempered martinsite. You noticed the conventionally made steel has large blocky carbides, which makes it more difficult to machine a knife. What will happen is if I am machining this and the large carbide is present, the carbide can come out and you get either what looks like a chip or the surface finish doesn’t look very good. Secondly, the large carbides are not very tough so you can get edge chipping. If you look at the CPM picture first thing you notice is that all of the carbides are all very finely dispersed. The percentage volume of carbide in each of these pictures is the same, so having finely dispersed carbides helps toughness or resistance to breakage and wear resistance. You can heat treat them both at the same hardness level, but CPM is going to be tougher, it’s going to have better wear resistance and it’s easier to manufacture for the knife maker. So those are, to me, the three most critical important things of CPM over conventionally made steels.
KnifeArt: So, when people ask what is the best steel for knives what is your response?
Beckman: I don’t have an answer to that, but the way I would answer the question is; What does the knife maker want to accomplish? How hard is the knife? Do they need a corrosion resistance knife? What kind of knife are they making? What is the use of it? And then what are they comfortable with? For example; if a knife maker’s whole experience has been 1095 carbon steel or low alloy tool steel, to jump into one of the very highly alloyed CPM grades would be very difficult for that person to heat treat and to process. It depends on what the knife maker is comfortable with and wants so accomplish.
KnifeArt: That is great, what recommendations do you have for someone in the knife industry, a knife maker or a knife collector or a knife enthusiast when looking at a data sheet that Crucible or any knife company produces for their steel?
Beckman: The purpose of the steel datasheets is not really geared to a knife maker or consumer. They are geared to other industrial markets and engineers; like machine punches, industrial cutting tools and plastics market. If I am a knife maker probably the most important thing they need to know how to do is the heat treatment. So the datasheets will give some guidelines on how to heat treat. What you will find is with high alloy steels they require a much more sophisticated and complicated heat treatment process. You just can’t put it in an oven, pull it out of the oven, stick it in a pot of water or let it air cool and hope its okay.
You will see in the data sheets there will be various temperatures for austentizing that will give you a certain range and quenched hardness. Generally speaking if you really want to make a knife that focuses on toughness you do a little lower austentizing temperature. If you want to make another knife that is fully focused on wear resistance you do a higher austentizing temperature and then you temper into whatever hardness range you want, so that is a decision that a knife maker has to make. My suggestion would be to always look on the blogs and learn what other people do. You will see properties on datasheets regarding hardness and toughness and wear resistance verses some other alloys and its nice to know, but a lot of the discussion is because its a tight community and there is a lot of information shared on the web and on blogs, and that is as important or more important than datasheets.
KnifeArt: What were the characteristics for a good knife steel?
Beckman: If I look at the property of hardness, how hard do you want to make it? Should the steel have some degree of corrosion resistance or not? The four basic properties are hardness, corrosion resistance, toughness and wear resistance.
KnifeArt: Can you talk about the advantages and disadvantages of carbon steel versus stainless steel?
Beckman: I think the two advantages of carbon steel are that it is less expensive to buy the carbon steel blade and it is easier to make a knife with carbon steel. Those are the benefits of carbon steel. The cost and the corrosion resistance of stainless steel are the two biggest things. The benefits of stainless are ease of maintenance but at a higher cost and increased manufacturing difficulty.
KnifeArt: When a knife buyer looks at CPM steels, a lot of them are using 154CM, S30V or S35V or S90V, S110V also S125V. That is a wide range of CPM steels being used in the knife industry and there are other carbon steels as well. What is your recommendation as the manufacturer when a knife buyer is looking at all of these different steels?
Beckman: The first question I ask and it’s the same question I always ask a cutting tool maker- what do you currently use? And then, is it failing? Or, what do you want to get out of your steel? Because it gets back to what their experience is. People want to change grades; either they need to upgrade because they want to make a better product or the product they are making failed- maybe breaks, chips, or corrodes and so they want to upgrade to get better performance. Better performance and better products sound like they are the same thing but sometimes they are not, so I’m always asking where are you today and then sometimes I will just say here is the family. Get on the blogs, and you get some tremendous forums that I have never seen in any other industry. That’s where all the trial and errors are discussed. I would say if someone is doing a certain heat treatment and I ask the question, does it work? And if the person says yup it makes a good knife then I say keep doing it, don’t change and don’t let the engineers get in the way of success.
KnifeArt: Can you talk about the hardness of a knife blade and how that impacts it’s performance?
Beckman: Okay, harder is always not better in any material. Just because you might think, get it as hard as I can because harder is better, that is not true when you are talking about the best combination of properties. You pick a hardness that works. You really don’t want anything harder than it should be because you want some combination of toughness and wear resistance. For the hardness in carbon steel, the harder it is, the more wear resistant it’s going to be. In CPM steels because of all the vanadium carbide, harder is not necessarily better.
For example I can have a CPM 10V at Rockwell C61 and I can have a conventional D2 at Rockwell C64, the 10V will have better wear resistance because of the vanadium carbides even though it’s a 3 point lower hardness. And it will be tougher, so you only should make it as hard as it needs to be. You gain the properties of toughness and wear resistance- let the vanadium carbides work for you.
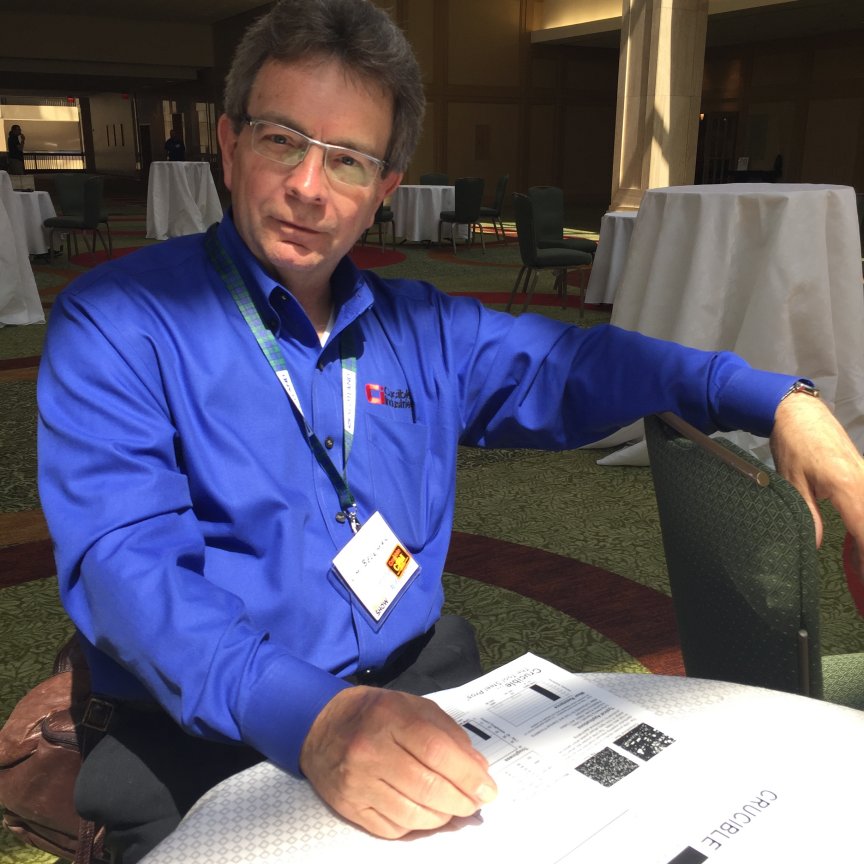